Za zgodą Jerzego Kulińskiego
Niektóre fragmenty instrukcji składania silnika mogą na pierwszy rzut oka wydać się przesadne. Niech Was nie zmyli retoryka kolejnej pogadanki Tadeusza Lisa. On sobie pozwala na żarty, ale tam gdzie potrzeba – stawia sprawę ostro. Jak pisze, że do montażu silnika będzie potrzebny biały obrus lub prześcieradło oraz arkusze polietylenowej folli bąbelkowej, to nie rezonujcie. Widać tak trzeba.
Przypominają mi się czasy pracy na budowie. Podczas gdy absolutna większość kierowników budów zwracała się do robotników i brygadzistów (ale już nie do majstrów) nie tylko głośno, nie tylko „per ty”, ale i nie rzadko w oprawie „grubego słowa” – mój przyjaciel kierownik (i żeglarz!) z sąsiedzkiej budowy z personelem rozmawiał bardzo cicho. Wydawane przez niego polecenia zazwyczaj miałe formę pytania – panie Formela, czy mógłby pan zrobić to i tamto? Nie zdarzyło się, aby indagowany przez kierownika robotnik „nie mógłby”. Im kierownik był bardziej zły – tym ciszej mówił.
Tak więc – nie lekceważcie niby żartobliwych sugestii Tadeusza. To są rady udzielane z dobrego serca i znajomości tematu 🙂
Żyjcie wiecznie !
Don Jorge
—————————————————————–
Doszliśmy do etapu, kiedy wszystkie elementy silnika zostały zregenerowane i przed Wami jego montaż. To najprzyjemniejsza i najbardziej odpowiedzialna część pracy.
Jeżeli robicie to pierwszy raz, to zainwestujcie skrzyneczkę dobrze schłodzonego piwa w nadzór doświadczonego mechanika od dowolnych silników wysokoprężnych – który przyniesie ze sobą potrzebne Wam narzędzia specjalistyczne – głównie klucze dynamometryczne oraz opaskę ułatwiającą włożenie do cylindra tłoka z założonymi pierścieniami.
Od czego zaczynamy? Od wydrukowania w formacie minimum 13×18 (lepiej 18 x 24) fotografii z demontażu silnika. Nie liczcie tutaj na Waszą dobrą pamięć i zgadywanie znane z puzzli! Wierzcie mi na słowo, że przy składaniu silnika wyjątkowo sprawdza się stare powiedzenie: najkrótszy ołówek jest sto razy lepszy niż najdłuższa pamięć…
Na wejściu potrzebujecie dwóch mocnych stołów – brudnego i montażowego. Brudny, z wanienką służy do mycia części- montażowy przykryjecie czystym, spranym prześcieradłem. Wiem, że doświadczeni mechanicy odniosą się do tego z politowaniem. Znam nawet takiego, który gdy podniosłem choinkę ze skrzyni biegów która zaolejona upadła mu w piach i poszedłem, żeby ją starannie umyć, popatrzył na mnie ze zdumieniem i powiedział: daj spokój Tadzik – to się i tak u klyenta na mąkie zemle…
Ale Wy robicie to pierwszy raz – i na jasnym, czystym prześcieradle od razu zobaczycie, gdy Wam wypadnie malutki klin napędu pompy olejowej lub miniaturowa sprężynka regulatora odśrodkowego pompy wtryskowej (Boże uchowaj! Amen).
Każdy silnik generalnie składamy w kolejności odwrotnej niż go rozbieraliśmy – ponumerowane zdjęcia w formie rozkładanego kalendarza na ścianie są bezcenne. Nie będziemy tutaj opisywać po kolei wszystkich operacji (po to wykonaliście sesję zdjęciową przy rozbieraniu silnika), ale skupimy się na krytycznie ważnych czynnikach sukcesu, które zadecydują o tym, czy będziecie mieli perfekcyjny napęd na jachcie, czy też niekoniecznie lub co najwyżej coś porównywalnego z napędem zdjętym z półki.
Właściwą pracę zaczynamy od starannego umycia dwóch krytycznie ważnych części – wału korbowego oraz bloku silnika. Teoretycznie wał powinien wrócić czysty z obróbki mechanicznej. Ale długoletnia praktyka warsztatowa mówi, że czasami wraca, a czasami nie. Niekiedy płucząc acetonem kanały olejowe z przerażeniem stwierdzicie, że z otworków wypłynęły nie tylko resztki starego oleju, ale też małe stalowe wiórki – które w oka mgnieniu potrafią uszkodzić delikatne, miękkie powierzchnie panewek. Mogą się tam dostać wraz z chłodziwem maszyny szlifierskiej – tak, czy tak, lepiej załóżcie że kanalikach olejowych siedzi złe i lepiej je stamtąd wygonić. Oto trick warsztatowy pokazany na fotografii (patrz podpis). Zwróćcie uwagę, że wykonuje płukanie na foli bąbelkowej. To nie przypadek. Te błyszczące, okrągłe powierzchnie to utwardzane i szlifowane tarcze podpór wału. Przenoszą nie małe obciążenia – zwłaszcza, gdy silnik pracuje na wolnych obrotach z dużym obciążeniem. Mała rysa na nich może wywołać ich pęknięcie na skutek zjawiska karbu. Tak ukręcił nam się wał z podrasowanym mocno silniku gokarta. Ryska była maleńka – powstała gdy koledze wymknęły się z ręki szczypce do pierścieni Segera. Była tak mała, że wypatrzyliśmy ją dopiero przez okulary pożyczone od asystującego nam dalekowidza. No i machnęliśmy na nią ręką przed zawodami, bo i tak byliśmy wykończeni. Przy czwartym starcie (z pięciu) wał się ukręcił – został idealnie ścięty wzdłuż tej rysy….
Wał można by też przepłukać agregatem wysokociśnieniowym – ale zazwyczaj trzeba wtedy dotoczyć dedykowaną końcówkę o małej średnicy.
Agregatu ciśnieniowego użyjemy do przepłukania kanałów wodnych i olejowych silnika. Musicie mieć świadomość, że po dłuższym okresie eksploatacji w silniku na ściankach przewodów olejowych osadza się szlam z dużą zawartością sadzy (nawet jeśli przestrzegacie sezonowych wymian oleju). Gdy odstawiacie maszynę lotne cząstki odparowują, a stałe zgrzewają się do ścianek kanałów – ich światło się systematycznie zmniejsza. Teraz przywracamy ich parametry pierwotne. Nie zdziwcie się, gdy wypłuczecie coś, co wygląda na okruchy twardego, czarnego ebonitu – to jest właśnie zgorzel olejowa, częsta w silnikach, które miały awarię układu chłodzenia – zwłaszcza gdy doszło do jego zatarcia na skutek przegrzania.
Jeżeli robicie to pierwszy raz, to zainwestujcie skrzyneczkę dobrze schłodzonego piwa w nadzór doświadczonego mechanika od dowolnych silników wysokoprężnych – który przyniesie ze sobą potrzebne Wam narzędzia specjalistyczne – głównie klucze dynamometryczne oraz opaskę ułatwiającą włożenie do cylindra tłoka z założonymi pierścieniami.
Od czego zaczynamy? Od wydrukowania w formacie minimum 13×18 (lepiej 18 x 24) fotografii z demontażu silnika. Nie liczcie tutaj na Waszą dobrą pamięć i zgadywanie znane z puzzli! Wierzcie mi na słowo, że przy składaniu silnika wyjątkowo sprawdza się stare powiedzenie: najkrótszy ołówek jest sto razy lepszy niż najdłuższa pamięć…
Na wejściu potrzebujecie dwóch mocnych stołów – brudnego i montażowego. Brudny, z wanienką służy do mycia części- montażowy przykryjecie czystym, spranym prześcieradłem. Wiem, że doświadczeni mechanicy odniosą się do tego z politowaniem. Znam nawet takiego, który gdy podniosłem choinkę ze skrzyni biegów która zaolejona upadła mu w piach i poszedłem, żeby ją starannie umyć, popatrzył na mnie ze zdumieniem i powiedział: daj spokój Tadzik – to się i tak u klyenta na mąkie zemle…
Ale Wy robicie to pierwszy raz – i na jasnym, czystym prześcieradle od razu zobaczycie, gdy Wam wypadnie malutki klin napędu pompy olejowej lub miniaturowa sprężynka regulatora odśrodkowego pompy wtryskowej (Boże uchowaj! Amen).
Każdy silnik generalnie składamy w kolejności odwrotnej niż go rozbieraliśmy – ponumerowane zdjęcia w formie rozkładanego kalendarza na ścianie są bezcenne. Nie będziemy tutaj opisywać po kolei wszystkich operacji (po to wykonaliście sesję zdjęciową przy rozbieraniu silnika), ale skupimy się na krytycznie ważnych czynnikach sukcesu, które zadecydują o tym, czy będziecie mieli perfekcyjny napęd na jachcie, czy też niekoniecznie lub co najwyżej coś porównywalnego z napędem zdjętym z półki.
Właściwą pracę zaczynamy od starannego umycia dwóch krytycznie ważnych części – wału korbowego oraz bloku silnika. Teoretycznie wał powinien wrócić czysty z obróbki mechanicznej. Ale długoletnia praktyka warsztatowa mówi, że czasami wraca, a czasami nie. Niekiedy płucząc acetonem kanały olejowe z przerażeniem stwierdzicie, że z otworków wypłynęły nie tylko resztki starego oleju, ale też małe stalowe wiórki – które w oka mgnieniu potrafią uszkodzić delikatne, miękkie powierzchnie panewek. Mogą się tam dostać wraz z chłodziwem maszyny szlifierskiej – tak, czy tak, lepiej załóżcie że kanalikach olejowych siedzi złe i lepiej je stamtąd wygonić. Oto trick warsztatowy pokazany na fotografii (patrz podpis). Zwróćcie uwagę, że wykonuje płukanie na foli bąbelkowej. To nie przypadek. Te błyszczące, okrągłe powierzchnie to utwardzane i szlifowane tarcze podpór wału. Przenoszą nie małe obciążenia – zwłaszcza, gdy silnik pracuje na wolnych obrotach z dużym obciążeniem. Mała rysa na nich może wywołać ich pęknięcie na skutek zjawiska karbu. Tak ukręcił nam się wał z podrasowanym mocno silniku gokarta. Ryska była maleńka – powstała gdy koledze wymknęły się z ręki szczypce do pierścieni Segera. Była tak mała, że wypatrzyliśmy ją dopiero przez okulary pożyczone od asystującego nam dalekowidza. No i machnęliśmy na nią ręką przed zawodami, bo i tak byliśmy wykończeni. Przy czwartym starcie (z pięciu) wał się ukręcił – został idealnie ścięty wzdłuż tej rysy….
Wał można by też przepłukać agregatem wysokociśnieniowym – ale zazwyczaj trzeba wtedy dotoczyć dedykowaną końcówkę o małej średnicy.
Agregatu ciśnieniowego użyjemy do przepłukania kanałów wodnych i olejowych silnika. Musicie mieć świadomość, że po dłuższym okresie eksploatacji w silniku na ściankach przewodów olejowych osadza się szlam z dużą zawartością sadzy (nawet jeśli przestrzegacie sezonowych wymian oleju). Gdy odstawiacie maszynę lotne cząstki odparowują, a stałe zgrzewają się do ścianek kanałów – ich światło się systematycznie zmniejsza. Teraz przywracamy ich parametry pierwotne. Nie zdziwcie się, gdy wypłuczecie coś, co wygląda na okruchy twardego, czarnego ebonitu – to jest właśnie zgorzel olejowa, częsta w silnikach, które miały awarię układu chłodzenia – zwłaszcza gdy doszło do jego zatarcia na skutek przegrzania.
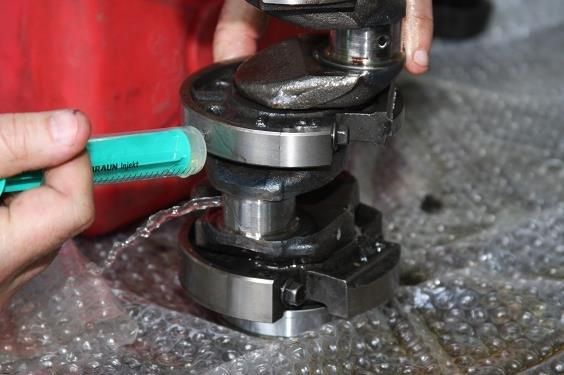
.
W czysty blok stojący na stole montażowym wsuwamy wał (w tym typie silnika – gdzie nie występuje podział skrzyni korbowej). Musi wejść absolutnie gładko – jeżeli nie chce, to coś jest nie tak. Ale to się prawie nie zdarza – wystarczy go delikatnie obrócić w prawo i w lewo i wszystkie podpory powinny wskoczyć na swoje miejsce.
W czysty blok stojący na stole montażowym wsuwamy wał (w tym typie silnika – gdzie nie występuje podział skrzyni korbowej). Musi wejść absolutnie gładko – jeżeli nie chce, to coś jest nie tak. Ale to się prawie nie zdarza – wystarczy go delikatnie obrócić w prawo i w lewo i wszystkie podpory powinny wskoczyć na swoje miejsce.
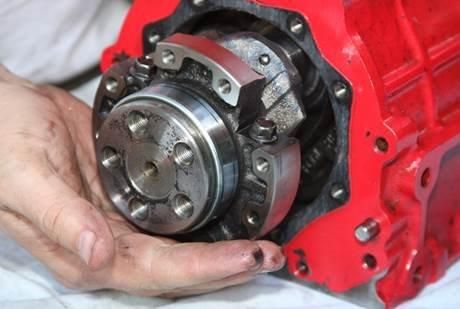
.
Zanim zrobimy cokolwiek innego musimy ustabilizować wał – to kręgosłup silnika. Zarówno podpory wału jak i panewki główne dokręcamy koniecznie kluczem dynamometrycznym – wartościami momentów, które odczytaliśmy z instrukcji serwisowej. Reguła jest taka – jeżeli zażyczyliście sobie (przy dorabianych panewkach) zrobienia ich w ciasnej tolerancji, to dokręcacie je minimalnym momentem, jeżeli odwrotnie – to momentem maksymalnym przewidzianym przez instrukcję. Panewki muszą być przed montażem posmarowane olejem lub cienką warstwą smaru typu towot. Chodzi o to, aby przy pierwszym uruchomieniu nawet na moment nie wystąpiło suche tarcie w układzie wał-panewka. Przy montażu panewek, zarówno głównych, jak i korbowodowych zwróćcie koniecznie uwagę na to, żeby małe przetłoczenie panewki (zamki) widoczne na pierwszym planie znalazły się konieczne w właściwych gniazdach podpór. Jeżeli będzie inaczej ten błąd jest śmiertelny dla Waszego silnika. Panewka obróci się i minie z otworem olejowym w wale lub bloku – zniszczenie silnika jest kwestią minut. Ale sądzę, że zrobicie to bezbłędnie nawet za pierwszym razem.
Zanim zrobimy cokolwiek innego musimy ustabilizować wał – to kręgosłup silnika. Zarówno podpory wału jak i panewki główne dokręcamy koniecznie kluczem dynamometrycznym – wartościami momentów, które odczytaliśmy z instrukcji serwisowej. Reguła jest taka – jeżeli zażyczyliście sobie (przy dorabianych panewkach) zrobienia ich w ciasnej tolerancji, to dokręcacie je minimalnym momentem, jeżeli odwrotnie – to momentem maksymalnym przewidzianym przez instrukcję. Panewki muszą być przed montażem posmarowane olejem lub cienką warstwą smaru typu towot. Chodzi o to, aby przy pierwszym uruchomieniu nawet na moment nie wystąpiło suche tarcie w układzie wał-panewka. Przy montażu panewek, zarówno głównych, jak i korbowodowych zwróćcie koniecznie uwagę na to, żeby małe przetłoczenie panewki (zamki) widoczne na pierwszym planie znalazły się konieczne w właściwych gniazdach podpór. Jeżeli będzie inaczej ten błąd jest śmiertelny dla Waszego silnika. Panewka obróci się i minie z otworem olejowym w wale lub bloku – zniszczenie silnika jest kwestią minut. Ale sądzę, że zrobicie to bezbłędnie nawet za pierwszym razem.
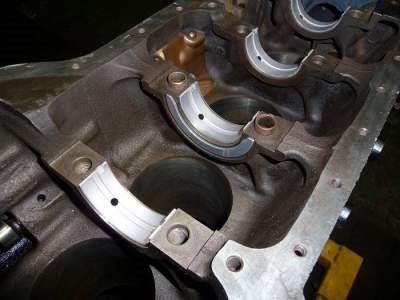
.
Złożony wał (na głównych podporach) musi się dać obracać ręką bez większego wysiłku i idealnie gładko w całym zakresie obrotu. Sprawdzenie wykonujecie ZANIM ZAŁOŻYCIE PRZEDNI USZCZELNIAĆ I ZAMONTUJECIE KORBOWODY.
Teraz włożymy tłoki. W tym typie silnika da się je włożyć od góry, ponieważ konstruktorzy zadbali o to, aby szerokość stopy korbowodu była mniejsza niż średnica cylindra – jeżeli jest inaczej to tłoki montujemy przed montażem wału.
Jak pewnie założyć pierścienie – bez obawy ich uszkodzenia? Najlepiej jest użyć specjalnych szczypiec, takich jak na fotografii.
Złożony wał (na głównych podporach) musi się dać obracać ręką bez większego wysiłku i idealnie gładko w całym zakresie obrotu. Sprawdzenie wykonujecie ZANIM ZAŁOŻYCIE PRZEDNI USZCZELNIAĆ I ZAMONTUJECIE KORBOWODY.
Teraz włożymy tłoki. W tym typie silnika da się je włożyć od góry, ponieważ konstruktorzy zadbali o to, aby szerokość stopy korbowodu była mniejsza niż średnica cylindra – jeżeli jest inaczej to tłoki montujemy przed montażem wału.
Jak pewnie założyć pierścienie – bez obawy ich uszkodzenia? Najlepiej jest użyć specjalnych szczypiec, takich jak na fotografii.
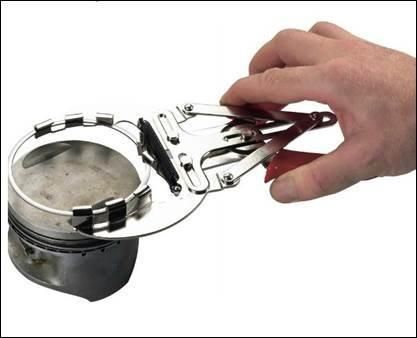
.
Ale jeśli ich nie macie, to kupcie za 6 zł szczelinomierz na Allegro i użyjcie z niego blaszek jako prowadzeń – oczywiście pamiętając o tym, aby zacząć od najniższego pierścienia olejowego. Nie starajcie się rozginać pierścieni palcami. Prawie na pewno je połamiecie – a jeżeli były za miękkie i udało Wam się je trwale rozgiąć, to wrzućcie je do śmietnika.
Osadzacie tłok w cylindrze. Ale teraz ważny trick warsztatowy. Trzeba cholernie uważać, aby nie porysować śrubami stopy korbowodu delikatnej gładzi cylindra. Można je zabezpieczyć albo taśmą malarską, albo lepiej – nasuniętymi kawałkami rurki paliwowej.
Ale jeśli ich nie macie, to kupcie za 6 zł szczelinomierz na Allegro i użyjcie z niego blaszek jako prowadzeń – oczywiście pamiętając o tym, aby zacząć od najniższego pierścienia olejowego. Nie starajcie się rozginać pierścieni palcami. Prawie na pewno je połamiecie – a jeżeli były za miękkie i udało Wam się je trwale rozgiąć, to wrzućcie je do śmietnika.
Osadzacie tłok w cylindrze. Ale teraz ważny trick warsztatowy. Trzeba cholernie uważać, aby nie porysować śrubami stopy korbowodu delikatnej gładzi cylindra. Można je zabezpieczyć albo taśmą malarską, albo lepiej – nasuniętymi kawałkami rurki paliwowej.
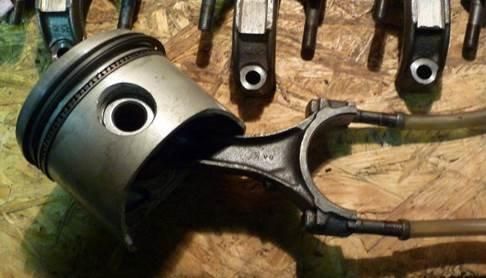
.
Ten prosty i tani przyrząd pozwoli Wam bez problemu wsunąć tłok z założonymi pierścieniami do cylindra, uprzednio posmarowanego olejem. Jeżeli go nie macie to zaimprowizujcie go z kawałka blachy stalowej i dwóch cybantów o odpowiedniej średnicy. Ale jest tani i lepiej mieć go na jachcie z kompletem zapasowych pierścieni, panewek i uszczelek.
Ten prosty i tani przyrząd pozwoli Wam bez problemu wsunąć tłok z założonymi pierścieniami do cylindra, uprzednio posmarowanego olejem. Jeżeli go nie macie to zaimprowizujcie go z kawałka blachy stalowej i dwóch cybantów o odpowiedniej średnicy. Ale jest tani i lepiej mieć go na jachcie z kompletem zapasowych pierścieni, panewek i uszczelek.
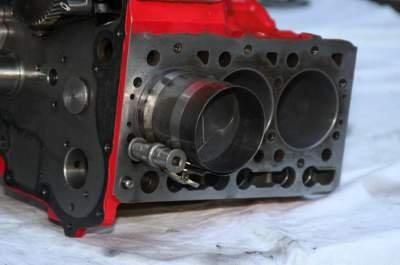
.
W razie nieszczęścia zatarcia silnika w długim rejsie, po tym ćwiczeniu poradzicie sobie z jego naprawą nawet w morzu. Będzie o tym w osobnym artykule, gdzie pokażemy, że możliwe jest poradzenie sobie (pod pewnymi warunkami) nawet z drobnymi pęknięciami bloku lub głowicy. Po przykręceniu panewek korbowodowych (mocujące je półmostki nazywane są w żargonie warsztatowym kapami) mamy praktycznie zmontowany układ korbowo-tłokowy.
Teraz będzie już z górki. Gumowym młotkiem osadzamy nowy pierścień Simmera przedniego uszczelniacza wału.
W razie nieszczęścia zatarcia silnika w długim rejsie, po tym ćwiczeniu poradzicie sobie z jego naprawą nawet w morzu. Będzie o tym w osobnym artykule, gdzie pokażemy, że możliwe jest poradzenie sobie (pod pewnymi warunkami) nawet z drobnymi pęknięciami bloku lub głowicy. Po przykręceniu panewek korbowodowych (mocujące je półmostki nazywane są w żargonie warsztatowym kapami) mamy praktycznie zmontowany układ korbowo-tłokowy.
Teraz będzie już z górki. Gumowym młotkiem osadzamy nowy pierścień Simmera przedniego uszczelniacza wału.

.
Jednak nie montujemy jeszcze koła zamachowego – z każdym ruchem silnik staje się coraz cięższy, a jest jeszcze sporo rzeczy do zrobienia wymagających przemieszczania silnika. Montujemy wałek rozrządu i przystępujemy do montażu jego napędu. Jeżeli jesteście zmęczeni, to przełóżcie tę operację na następny dzień – musicie być wypoczęci, a oświetlenie powinno być najlepiej naturalne. Jeżeli sztuczne, to wielopunktowe. Składamy rozrząd, z fotografii i oznakowanych pudełek odtwarzając wszystkie niezbędne podkładki dystansowe. Dzięki temu, że wcześniej zadbaliśmy o nabicie właściwych znaków na kołach przeniesienia napędu nie powinno być żadnych problemów. Kluczem dynamometrycznym dokręcamy nakrętki mocujące i zabezpieczamy je tak, jak to przewidział producent – zazwyczaj blaszaną podkładką z doginanym zębem. Przeniesienie napędu kołami łańcuchowymi jest typowe dla bardzo wytrzymałych silników przemysłowych.
Ważna uwaga, gdy macie do czynienia z silnikiem, w którym do przeniesienia napędu zastosowano łańcuch. Nawet nowy ma on pewien luz, gdyż inaczej nie dałby się założyć. Jest rzeczą konieczną, abyście po jego zmontowaniu założyli klucz z grzechotką na dolną śrubę mocującą główne koło pasowe do wału i wykonali kilkanaście pełnych obrotów – KONIECZNIE ZGODNIE Z KIERUNKIEM PRACY SILNIKA. Kontrolujecie czy znaki na kole dolnym wału oraz kole górnym wałka rozrządu zgrywają się za każdym obrotem ze znakami. Tak na marginesie, jeżeli silnik ma nieznany przebieg to ponieważ to ma być WASZ SILNIK – sugeruję, abyście przy okazji remontu kapitalnego wymienili cały napęd – to znaczy koła zębate, łańcuch oraz ewentualnie ślizgacz napinacza. Uważajcie na rady starych fachowców opowiadających legendy o niezniszczalnych łańcuchach. Jest w tym ziarno prawdy – gdyż legenda ukształtowała się na silnikach montowanych w Mercedesach W123, których napędy rozrządu wytrzymują 600-700 tys. Ale już mój ulubiony, śliczny 1.3 Multijet Fiata (stał się jednostką bazową dedykowanego napędu w lekkim autku miejskim Żony) wytrzymuje bezpiecznie 150 tys., ale po tuningu uwzględniają styl jazdy kobiety mojego życia – wymieniam go co 80 tys. A ten wyrzucany do kosza w warsztacie ma wyraźne objawy zmęczenia ciężką służbą. Ale powiedzmy to sobie otwarcie w zamkniętym klubie żeglujących dżentelmenów – czyż nie są to naturalne koszty operacyjne temperamentu kobiety, o którym marzy każdy mężczyzna…
Rozrząd już poskładany, pokrywa z nową uszczelką założona – czas zamknąć silnik od dołu. Przykręcamy smok pompy olejowej (zabezpieczamy śruby) i przykręcamy miskę olejową. Teraz STOP – co zrobić gdy nie mamy gdzie kupić uszczelki miski olejowej? Jej dorobienie jest trudne, a drobne nieszczelności staną się koszmarem. To może poskładać ją na silikon? Pomysł jest niezły, ale trzeba uważać, bo za cienka warstwa nie uszczelni miski, a za gruba sprawi, że nadmiar wyciśnie się do środka i z dużym prawdopodobieństwem dostanie się gdzieś w najbardziej niepożądane miejsce silnika. Oto użyteczny trick warsztatowy.
Jednak nie montujemy jeszcze koła zamachowego – z każdym ruchem silnik staje się coraz cięższy, a jest jeszcze sporo rzeczy do zrobienia wymagających przemieszczania silnika. Montujemy wałek rozrządu i przystępujemy do montażu jego napędu. Jeżeli jesteście zmęczeni, to przełóżcie tę operację na następny dzień – musicie być wypoczęci, a oświetlenie powinno być najlepiej naturalne. Jeżeli sztuczne, to wielopunktowe. Składamy rozrząd, z fotografii i oznakowanych pudełek odtwarzając wszystkie niezbędne podkładki dystansowe. Dzięki temu, że wcześniej zadbaliśmy o nabicie właściwych znaków na kołach przeniesienia napędu nie powinno być żadnych problemów. Kluczem dynamometrycznym dokręcamy nakrętki mocujące i zabezpieczamy je tak, jak to przewidział producent – zazwyczaj blaszaną podkładką z doginanym zębem. Przeniesienie napędu kołami łańcuchowymi jest typowe dla bardzo wytrzymałych silników przemysłowych.
Ważna uwaga, gdy macie do czynienia z silnikiem, w którym do przeniesienia napędu zastosowano łańcuch. Nawet nowy ma on pewien luz, gdyż inaczej nie dałby się założyć. Jest rzeczą konieczną, abyście po jego zmontowaniu założyli klucz z grzechotką na dolną śrubę mocującą główne koło pasowe do wału i wykonali kilkanaście pełnych obrotów – KONIECZNIE ZGODNIE Z KIERUNKIEM PRACY SILNIKA. Kontrolujecie czy znaki na kole dolnym wału oraz kole górnym wałka rozrządu zgrywają się za każdym obrotem ze znakami. Tak na marginesie, jeżeli silnik ma nieznany przebieg to ponieważ to ma być WASZ SILNIK – sugeruję, abyście przy okazji remontu kapitalnego wymienili cały napęd – to znaczy koła zębate, łańcuch oraz ewentualnie ślizgacz napinacza. Uważajcie na rady starych fachowców opowiadających legendy o niezniszczalnych łańcuchach. Jest w tym ziarno prawdy – gdyż legenda ukształtowała się na silnikach montowanych w Mercedesach W123, których napędy rozrządu wytrzymują 600-700 tys. Ale już mój ulubiony, śliczny 1.3 Multijet Fiata (stał się jednostką bazową dedykowanego napędu w lekkim autku miejskim Żony) wytrzymuje bezpiecznie 150 tys., ale po tuningu uwzględniają styl jazdy kobiety mojego życia – wymieniam go co 80 tys. A ten wyrzucany do kosza w warsztacie ma wyraźne objawy zmęczenia ciężką służbą. Ale powiedzmy to sobie otwarcie w zamkniętym klubie żeglujących dżentelmenów – czyż nie są to naturalne koszty operacyjne temperamentu kobiety, o którym marzy każdy mężczyzna…
Rozrząd już poskładany, pokrywa z nową uszczelką założona – czas zamknąć silnik od dołu. Przykręcamy smok pompy olejowej (zabezpieczamy śruby) i przykręcamy miskę olejową. Teraz STOP – co zrobić gdy nie mamy gdzie kupić uszczelki miski olejowej? Jej dorobienie jest trudne, a drobne nieszczelności staną się koszmarem. To może poskładać ją na silikon? Pomysł jest niezły, ale trzeba uważać, bo za cienka warstwa nie uszczelni miski, a za gruba sprawi, że nadmiar wyciśnie się do środka i z dużym prawdopodobieństwem dostanie się gdzieś w najbardziej niepożądane miejsce silnika. Oto użyteczny trick warsztatowy.
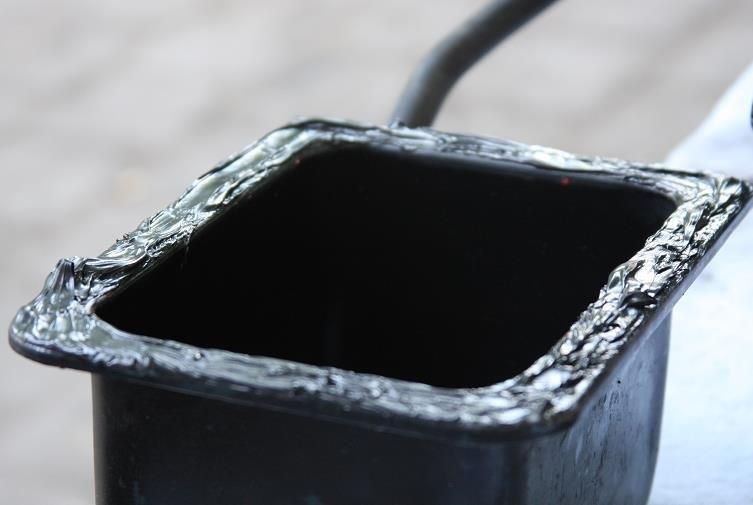
.
Nakładamy grubą warstwę czarnego silikonu na przylgnie miski olejowej, która w środku jest czysta i odtłuszczona acetonem. Czekamy aż nieco przeschnie. Nakładamy na krawędzie folię politylenową wywijając ją na zewnątrz i do wewnątrz oraz mocując jej wolne końce taśmą malarską do miski. Przedtem sprawdzimy, czy użyty silikon rzeczywiście nie klei się do polietylenu. Jeżeli się klei, to jako separatora możemy użyć tłustego papieru do wykładania foremek do pieczenia ciasta – jeden z dwóch powinien zawsze zadziałać. Przykręcamy miskę równomiernie, ale niezbyt silnie, tak, aby zostawić sobie jeszcze 1,5 -2 obrotów śruby (czyli typowo nieco ponad 2 mm grubości). Czekamy około 2 godzin na ukształtowanie się uszczelki. Teraz bardzo delikatnie usuwamy folię po odkręceniu miski i usuwamy skalpelem wypływki silikonu z obu stron. Mamy idealną uszczelkę przymocowaną trwale (jednostronnie) do miski – co najmniej kilkukrotnego użytku. W morzu lub obcym porcie bezcenne Teraz spryskujemy ją sprayem do zabezpieczenia uszczelek drzwiowych w zimie i montujemy już z właściwym dociskiem. Połączenie będzie rozbieralne i suche jak pieprz przez długie lata. I właśnie o to chodzi.
Jeszcze 2-3 godziny i kończycie. Montujemy popychacze, zakładamy uzbrojoną głowicę (o jej przykręcaniu pisałem już wcześniej), zakładamy pokrywę zaworów. Montujemy koła pasowe, pompy wody, alternator, rozrusznik i wymiennik ciepła. Oczywiście też kolektor wydechowy i zalany wstępnie filtr oleju. Przykręcamy koło zamachowe, tarczę sprzęgłową i jej obudowę. Przykręcamy skrzynkę przekładniową. Na koniec zmontujemy wtryskiwacze i świece żarowe. W ostatniej operacji zakładamy nowe węże gumowe i nowe opaski.
Na tym na dzisiaj kończymy. Zejdzie Wam na to prawie cały dzień. Ale tak musi być. Czy można to zrobić szybciej – można, tutaj chłopakom z Nebraski złożenie do podstaw typowej ośmiocylindrówki z Chevy (tak zwany SBC czyli small block) zajęło od startu do pierwszego odpalenia 17 minut 10 sekund (http://www.youtube.com/watch?v=OP2t_58OTeg ). Ale trzeba uwzględnić fakt, że to są studenci amatorzy. Zawodowy team Formuły 1 na moich oczach wykonał taką operację w czasie 10 minut. Posługiwali się jednak elektrycznymi narzędziami, w tym czasie nie zamienili ani jednego słowa…
W następnym odcinku – ostatnie muśnięcia i pierwszy start oraz strojenie silnika po remoncie na zaimprowizowanym stanowisku testowym.
Nakładamy grubą warstwę czarnego silikonu na przylgnie miski olejowej, która w środku jest czysta i odtłuszczona acetonem. Czekamy aż nieco przeschnie. Nakładamy na krawędzie folię politylenową wywijając ją na zewnątrz i do wewnątrz oraz mocując jej wolne końce taśmą malarską do miski. Przedtem sprawdzimy, czy użyty silikon rzeczywiście nie klei się do polietylenu. Jeżeli się klei, to jako separatora możemy użyć tłustego papieru do wykładania foremek do pieczenia ciasta – jeden z dwóch powinien zawsze zadziałać. Przykręcamy miskę równomiernie, ale niezbyt silnie, tak, aby zostawić sobie jeszcze 1,5 -2 obrotów śruby (czyli typowo nieco ponad 2 mm grubości). Czekamy około 2 godzin na ukształtowanie się uszczelki. Teraz bardzo delikatnie usuwamy folię po odkręceniu miski i usuwamy skalpelem wypływki silikonu z obu stron. Mamy idealną uszczelkę przymocowaną trwale (jednostronnie) do miski – co najmniej kilkukrotnego użytku. W morzu lub obcym porcie bezcenne Teraz spryskujemy ją sprayem do zabezpieczenia uszczelek drzwiowych w zimie i montujemy już z właściwym dociskiem. Połączenie będzie rozbieralne i suche jak pieprz przez długie lata. I właśnie o to chodzi.
Jeszcze 2-3 godziny i kończycie. Montujemy popychacze, zakładamy uzbrojoną głowicę (o jej przykręcaniu pisałem już wcześniej), zakładamy pokrywę zaworów. Montujemy koła pasowe, pompy wody, alternator, rozrusznik i wymiennik ciepła. Oczywiście też kolektor wydechowy i zalany wstępnie filtr oleju. Przykręcamy koło zamachowe, tarczę sprzęgłową i jej obudowę. Przykręcamy skrzynkę przekładniową. Na koniec zmontujemy wtryskiwacze i świece żarowe. W ostatniej operacji zakładamy nowe węże gumowe i nowe opaski.
Na tym na dzisiaj kończymy. Zejdzie Wam na to prawie cały dzień. Ale tak musi być. Czy można to zrobić szybciej – można, tutaj chłopakom z Nebraski złożenie do podstaw typowej ośmiocylindrówki z Chevy (tak zwany SBC czyli small block) zajęło od startu do pierwszego odpalenia 17 minut 10 sekund (http://www.youtube.com/watch?v=OP2t_58OTeg ). Ale trzeba uwzględnić fakt, że to są studenci amatorzy. Zawodowy team Formuły 1 na moich oczach wykonał taką operację w czasie 10 minut. Posługiwali się jednak elektrycznymi narzędziami, w tym czasie nie zamienili ani jednego słowa…
W następnym odcinku – ostatnie muśnięcia i pierwszy start oraz strojenie silnika po remoncie na zaimprowizowanym stanowisku testowym.
.
Tadeusz
Źródło: www.kulinski.navsim.pl
Komentarze
Sign in
Witamy! Zaloguj się na swoje konto
Forgot your password? Get help
Password recovery
Odzyskaj swoje hasło
Hasło zostanie wysłane e-mailem.